Info:Pistons
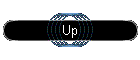
|
| |
Stroking Parts
The manufacturing process of pistons has changed considerably since the
inception of the internal combustion motor. Modern piston manufacturing is fully
automated with little or no human intervention.
This is not the case with JP Pistons.
JP Pistons strength lies in our ability to manufacture very low numbers of
pistons at a time (for example, 10-20). This ability means that we do not, and
cannot, compete with the massive automated facilities of the manufacturers of
mass produced pistons for modern vehicles. It also means that they cannot do
what we do either.
What is laid out below is the way that we make pistons. We use many modern
manufacturing processes, but also older methodologies which ensures our position
as a niche manufacturer.
Subjects
NOTE: The images here are all available in larger format, just click on the
image.
Foundry
The foundry is the beginning of the piston. At the foundry the die is prepared
by heating it to operating temperature for approximately one hour. This process
allows the die to readily accept the molten material when it is poured.

The material
The material used is a 10% silicon content aluminium.

The die
The dies used are 5 piece and three piece. These dies are made from cast iron
with steel inserts for the gudgeon pin holes and the cores. The cores dictate
the placement of the gudgeon pin and can be located to give offset pins or
square pins.

The process
The process starts by heating the material to 700 degrees Celsius. This is well
above the melting point of the aluminium, but below its boiling point. The
material is then scooped up with a ladle from the crucible (the pot that holds
the molten material). This is then poured into the die through the sprue. The
material is then allowed to cool before it is removed from the die and placed
into a bin of hot water. This water is used to facilitate a more even settling
of the hot metal.
After the castings have had time to cool they are placed into a heat treatment
plant overnight. This process tempers the casting and ensures the piston will
have improved qualities.
After it is removed from the heat treatment the casting has its runner removed.
This process takes little time and is fully automated.
Pin Boring
At this stage of the piston manufacturing process the casting has the gudgeon
pin hole rough machined and the locating bung machined.
The bung
This process is where the casting is machined on the base to allow placement of
the casting in other machines. This is carried out on a simple lathe.

The pin bore
Pin boring is done in conjunction with the bung turning, as one casting is
removed from having the bung face machined it is placed on the pin borer.
The pin borer is only a rough machining process which allows the reamer to enter
the gudgeon hole later.
CNC Turning
Turning of the casting is carried out on CNC (Computer Numeric Control)
machinery. This equipment is the most accurate and fastest available for this
application with very tight tolerances and extremely fast spindle speeds.
The castings are placed in the lathe on a bung and held in place by a solid rod
through the gudgeon pin hole. A draw bolt is activated in the chuck which draws
the rod toward the chuck and holds the piston in place.

The lathe is then started and the machining cycle begun. This cycle is
programmed into the lathe in a basic language called G-Code (this code is not
the only one available). G-Code has basic commands to tell the lathe to move to
certain positions (X,Y,Z co-ordinates), at particular spindle speeds (eg S2500
means spindle speed 2500rpm), at particular feed rates (eg G01; rapid traverse)
and other commands such as M01 (repeat programme) and others.
As you can see this is a simple system to learn and implement.
After the piston is machined it is removed from the lathe and the part number
stamped on the crown (top) of the piston.

The piston is now ready for the finishing processes.
Drilling
The first stages of the finishing process include drilling, slotting, valve and
crank relieving.
Drilling
Drilling includes all oil holes in places such as the gudgeon pin bosses and oil
ring grooves.
Slotting
Slotting is where slots are placed in the skirt or in the oil ring groove.
Valve relieving
This process is done on a mill and invloves setting the machine up for the
process, choosing the correct cutter and completing the job. Since there are so
many different types of valve reliefs it is impossible to have a specialised
machine set up to do one job.
Crank relieving
Crank releiving is carried out on a specialised machine which scallops the skirt
of the piston to the required shape and depth by using two opposed cutters
placed on a common shaft.
Grinding
This process involves
the final size being machined on the piston. The grinder machines the skirt of
the piston only and in the majority of cases is cam ground. Cam grinding ensures
the piston will "grow" evenly in the bore of the engine. A perfectly
round piston will expand unevenly during use because of the uneven placement of
material in the casting (gudgeon pin bosses and ribbing used for strengthening).
Reaming
The final machining
process for the piston is that of reaming. This process involves the piston
being placed in a bath of oil and reamed at different sizes to reach the final
size required. Since the pin boring process is only rough it is necessary to
ream the pin bore a number of times to achieve the surface finish and size
required. Reaming is not a fast process and is only partially automated (there
are automatic feeds on the reaming machines). Tolerances achieved on the
finished reamed surface is 0.4Ra.
Pin Fitting and Final Inspection
At this stage the piston is cleaned, fitted with the appropriate gudgeon pin,
stamped with the pistons' oversize and any other markings, and then sent to dispatch.
Dispatch
Finally, the piston is wrapped and placed in the shipping container with the
ring set and sent to the customer
|
| |
|